Several commonly used tools, materials classification
2016-03-04
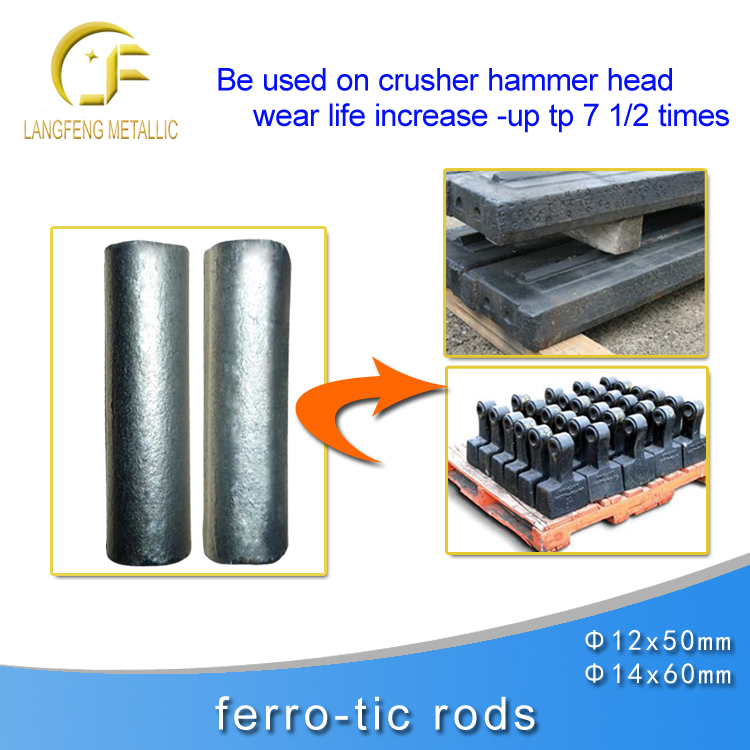
1 High-carbon steel :
High carbon steel tools is the amount of a 0.8% to 1.5% between the carbonaceous , After hardened use, due to the cutting of the friction four easily temper softening, be replaced by another high-speed steel cutting tools, etc. Generally only suitable for the cutting of the soft metal material , Common Ownership SK1, SK2 ,,,, SK7 like.
2 High-speed steel :
High-speed steel is a common name based alloy steel turning white, the carbon content of 0.7% to 0.85% of the carbon added to W, Cr, V, and so on Co alloy elements together.For example 18-4-4 high speed steel material containing 18% tungsten, 4% and 4% chromium vanadium high speed steel. Frictional heat generated in high-speed steel cutting tools can be up to 6000C, for at 1000rpm and threading of the following, commonly used high-speed steel tools such as SKH2, SKH4A, SKH5, SKH6, SKH9 like.
3 Non-iron alloy tool :
This is an alloy of cobalt, chromium and tungsten, because cutting is difficult to cast molding manufacturing, it is also known super-hard cast alloy, the most representative of stellite ,its tool toughness and excellent wear resistance at 8200C temperature its hardness remains unaffected, thermal extent far beyond high-speed steel, suitable for high speed and deep the cutting work.
4 Sintered carbide tools :
Carbide tool for the powder metallurgy products, mainly composed of tungsten carbide knives 50% to 90% tungsten, and adding titanium, molybdenum, tantalum, cobalt powder as a binder, and then sintered by heating to complete .Triple high hardness carbide tools than any other material, the most hard high-carbon steel, suitable for cutting hard metal or stone, because the material brittle, it can only be made from a sheet,and then welded to the more toughness on the handle, so the edge passivation or crack, you can replace the other blade or replace the blade, which is called throw-away enough turning tools.
Carbide tool by international standards (ISO) cut their different nature, is divided into P, M, K categories, and were blue, yellow and red colors to identify:
P class is suitable for cutting steel, there are P01, P10, P20, P30, P40, P50 six, P01 high-speed finishing tool, the number of small, high abrasion resistance, P50 low speed rough turning, large numbers, high toughness , handle painted blue to identify it .
K class is suitable for cutting stone, iron and other brittle materials, there is K01, K10, K20, K30, K40 five, K01 high speed finishing tool, K40 low speed rough turning such handle painted red to identify.
M class between the P and M class between classes, suitable for cutting larger materials such as toughness not? Unlined garment? Etc. Such coated with yellow handle to identify it.
Cutters are made of alumina ceramic powder, add a small number of elements, and then through the high temperature sintering from its hardness, heat resistance, cutting speed is higher than tungsten carbide, but because the crisp, it does not apply to non-c .
6 Diamond Tool
When used for advanced surface processing, using a circular blade edge or surface of industrial diamonds to light system. Obtain a smoother surface, mainly used for precision turning copper alloy or light alloy must be used when turning at high speed, the minimum required in 60 ~ 100m / min, usually 200 ~ 300m / min.
7 Boron oxide
A cubic boron oxide (CBN) in recent years to promote the material, hardness and wear resistance second only to diamond, this tool is suitable for machining hard, wear-resistant iron group alloys and nickel-based alloys, cobalt based alloys.
Stay tuned for detailed product information company official website: http://www.langfengmetallic.com/